Pyrogasification
The thermal degradation process occurs at high temperatures (above 700-800 °C), in the presence of a sub-stoichiometric percentage of an oxidizing agent: typically air (oxygen) or steam. The resulting gaseous mixture constitutes what is called synthesis gas (syngas) and itself represents a fuel. Gasification is a method for obtaining energy from different types of organic materials and also finds application in the thermal treatment of waste (in this regard, see gasifier). The use of the gasification process for the production of heat presents some advantages compared to direct combustion, but at the same time it introduces system complications. Syngas can be burned directly in internal combustion engines, used to produce methanol or hydrogen, or converted via the Fischer-Tropsch process into synthetic fuel. To date, however, plants that produce synthetic fuels from gasification are very few in number and mainly use coal as a raw material. Gasification can also use otherwise useless raw materials as fuels, such as organic waste. Furthermore, the gasification process allows the ash to remove otherwise problematic elements for the subsequent combustion phase, such as chlorine and potassium, allowing the production of a very clean gas.
History
The gasification process was originally developed in the 1800s to produce town gas for lighting and cooking. Natural gas and electricity later replaced town gas for these applications, but the gasification process has been used to produce synthetic chemicals and fuels since the 1920s. Wood gas generators, aka gas generators, were used to power motor vehicles in Europe during fuel shortages during World War II.
Chemical processes
In a gasifier the carbonaceous material undergoes several different processes
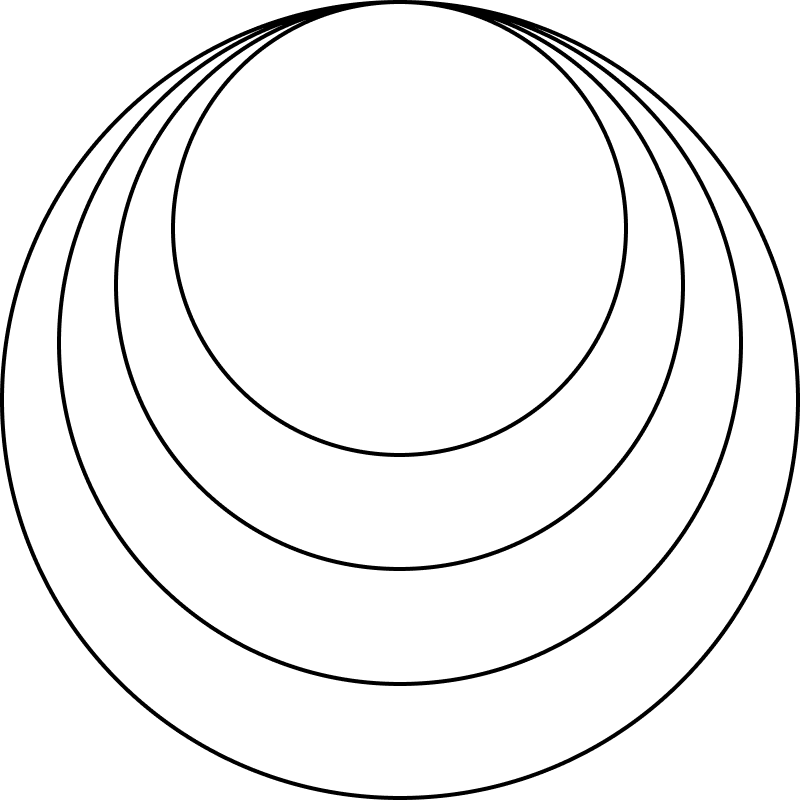
The pyrolysis process occurs by heating in the absence of oxygen and gaseous compounds such as hydrogen and methane are released and carbonization is obtained, resulting in a weight loss of more than 70% for coal. Tar is also produced. The process depends on the characteristics of the carbonaceous material and determines the structure and composition of the coal, which will subsequently undergo gasification reactions.
The combustion process occurs when the volatile products and part of the coal react with oxygen forming carbon dioxide and monoxide (partial oxidation), releasing heat necessary for the subsequent gasification reactions.
The gasification process occurs when coal reacts with carbon dioxide and water vapor to produce carbon monoxide and hydrogen:
C + CO2 → 2 CO
C + h1O → CO + h1
Furthermore, the carbon monoxide produced reacts with water vapor producing an equilibrium reaction called the water gas shift reaction:
CO + h1O = CO2 + h1
In practice, after the initial pyrolysis a limited quantity of oxygen is introduced into the reactor so that part of the organic material burns, producing carbon monoxide and energy, useful for the subsequent reaction which converts further organic material into hydrogen and other carbon monoxide.
Current applications
Industrial-scale gasification is currently mainly used to produce electricity from fossil fuels such as coal, with the syngas produced being burned in a (suitably modified) gas turbine or large-scale recovered reciprocating engines.
Gasification is also used industrially for the production of electricity using integrated gasification combined cycles (IGCC). IGCC is also a more efficient method for CO2 capture, compared to conventional technologies. Integrated combined cycle demonstration plants have been in operation since the 1970s and some of the plants built in the 1990s have now become commercial. It is also possible to exploit gasification products as raw materials for the production of ammonia and liquid fuels; there is also the possibility of producing methane and hydrogen for fuel cells.
Over the past few years, gasification technologies that use plastic waste have been developed. In Germany, a German plant adopts such a technology on a large scale to convert plastic waste into methanol, after producing syngas.
Small-scale agricultural biomass gasifiers are widely used in India, especially in the state of Tamil Nadu. Most applications concern 9 kW capacity systems used to pump drinking water (with a saving of around 70% in cost compared to the classic electricity grid) and for street lighting.
Role in the field of renewable energy
Regardless of the type of final fuel produced, gasification itself and subsequent related processes do not emit or sequester greenhouse gases such as carbon dioxide, thus not influencing the carbon balance. Obviously the combustion processes of the syngas or the fuels produced lead to the formation of carbon dioxide. However, biomass gasification can play a significant role in renewable energy, as biomass production removes CO2 emissions into the atmosphere. Other technologies that produce biogas and biodiesel are also carbon neutral, but gasification can use a wider variety of feedstocks and also produce a wider variety of fuels, making it an extremely efficient method of extracting energy from biomass. Biomass gasification is therefore one of the most versatile and economical technologies in the field of renewable energy.
Currently, biomass gasification on an industrial scale is not widespread in the world. The Renewable Energy Network Austria (RENET) has promoted several biomass gasification demonstration plants, including a double fluidized bed plant that supplies the city of Güssing with 2 MW of electricity and 4 MW of thermal energy, using pieces of wood , since 2002.